Hexagon Measurement SystemsNo matter what Hexagon measurement equipment or software you use, we want to hear your ideas and suggestions on how we can improve.
Thanks for your assistance in helping us shape the future. |

disallow invalid feature names
I would like, that PC-DMIS makes it impossible to use “invalid” characters (spaces or special characters) in feature names or at least warn the user when using them.
I have seen many problems come from it first hand and also countless forum threads about it.

I material specific illumination calibration that is interchangeable.
I would like to have the ability to change the illumination calibration without having to re-calibrate the illumination when I inspect a different type of material. At this time, if I calibrate the illumination to one type of material, then I can not use the same calibration on a different type of material as effectively. I would like to be able to toggle between the illumination calibrations.
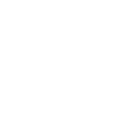
Send an email alert...
As of yesterday, I'm now programming in an office at the opposite end of the factory to the CMM.
The operator isn't always at the CMM especially if it is a long program.
Could PC-DMIS be set to send an email out to specified users when:
1) the program stops when the probe crashes
2) the probe needs manually removing/inserting
3) the program reaches the end

General toleranc classes (maps)
Now when I insert distance dimensions I have to write down the nominal value and tolerance for each dimension. I would like to see PC-DMIS fill the tolerance zones according to nominal dimension (if I choose it; checkbox) and chosen standard (ISO 2768, DIN16742 TG1-TG8, ISO 16901, ...) (PC-DMIS remember chosen standard within program). Something similar is in Location dimensions but it is only for holes and shafts. I also miss a tool or manual to create my own tolerance maps for standards we used and common tolerances on drawings ( +/- 0.05mm; +/- 0.1mm;+/- 0.2mm;+/- 0.3mm). To sum what I want, more flexibility and automation filling the tolerances for distance and location dimensions.
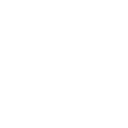
Changing the vector approach on a Circle
It would be nice to add a 3d vector approach in auto circle, to measure circles on cone, sphere... without doing it by autovector points.

I would like to be able to change a contact auto feature into a vision one (and vice versa) without having to delete the feature and recreate it
It would be a good time saver to not need to reprogram if there was a toggle parameter in the edit window for auto features for sensor type
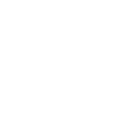
Save function as a PC-DMIS Command
As a PC-DMIS user, it would be an advantage to have a save function in PC-DMIS. Sometimes users are using VB to save the measurement routine. It would be nice if there is a function in PC-DMIS to have a commando in your measurement routine which functions as a Save Routine.

Add the ability to resize report snapshots

Inspect Realtime Report Window
Allow realtime Report Window within Inspect, I do not want to have to create slideshows for 2,000 programs.
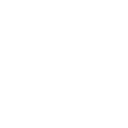
Report concave/convex condition of planes
ability to evaluate if a plane is either concave or convex.
Servicio de atención al cliente por UserEcho