Hexagon Measurement SystemsNo matter what Hexagon measurement equipment or software you use, we want to hear your ideas and suggestions on how we can improve.
Thanks for your assistance in helping us shape the future. |

Ability to adjust the vector of an avoidance move
In addition to being able to separately adjust the distance of avoidance moves, it would be nice to control the vector of an avoidance move.
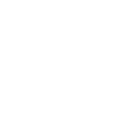
CREATING A WIDTH AUTOMATIC USING THE AUTO SLOT MEASURMENT
If I can create a slot or a circle relative to a plane than why can't I create a width in the same manner. Why should I have to create additional alignments. Example: I have a project that has 60 slots most of which are used as datum features. Creating 120 widths and 60 additional alignments in a program is not practical. Secondly, Why can't I use the points that make up the auto slot measurement and have pcdmis create widths using those points automatically ? Something else to consider is that all of these slots are drafted with no parallel sides.
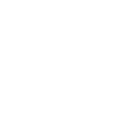
Inserting a feature into an argument list
Inserting a feature into the beginning or middle of an argument list, PC-DMIS doesn't parse the string as it's pasted and thinks the existing name is getting lengthened, even if a comma is present. When creating a FEAT/SET, I needed to include individual hits. I started with the dialog box and selected PNT3. It needed to be the 3rd point in the list, but it was the easiest to select. The feature set was:
CONSTR/SET,BASIC,PNT3,,
Then I was told I needed to change it so it explicitly brought in the single hit
CONSTR/SET,PNT3.HIT[1],,
Then I needed to add the first 2 points from LIN_L in front of it in the list
CONSTR/SET,BASIC,LIN_L.HIT[1],LIN_L.HIT[2],PNT3.HIT[1],,
But this didn't squeeze 2 additional points in front PNT3. Instead, it changed the name of the single argument to 'LIN_L.HIT[1],LIN_L.HIT[2],PNT3.HIT[1]'. This behaves the same whether I paste the new names as strings, the them manually or use a combination of both.
It appears that PC-DMIS doesn't recognize the commas as delimiters when it's re-parsing the line after an edit. And it doesn't change the quantity of arguments unless the additions are at the end.
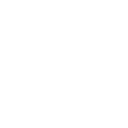
excel form report keep the Excels formatting/allow tables.
currently Excel form report clears out any formatted cell where the data will generate. Can we have it so it doesn't clear out the cells formatting or so the information will generate in a table inserted into the excel sheet.
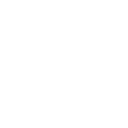
Probe simulation
Add manual probe simulation capability for off-line measurements preparing/testing/training.

Allow routines(s) to be scheduled to run at start of day - and block execution until run
From PC-DMIS Forum post
"Hello,
We have a pair of calibration programs that need to be run at the beginning of the day prior to running production. How could I automatically "lock up" the machine until the operator runs these programs? If there is a method of doing this in VBA, that would be ideal.
Thanks,
M"
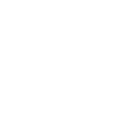
Dark Mode for Programming
Hello! I noticed that the latest version of PC-DMIS includes a dark mode feature. It applies to the home page and some options such as GT and setting up your datums inside a program but that is it. I use dark mode for everything when available. When you stare at a screen for over 8 hours a day, the white background for me personally is taxing. I would LOVE to have this feature available for the whole programming screen. Including the grey boxes/windows for features and the options at the top of the screen, and have a dark color scheme for the actual coding as well.
If this color scheme could be for the actual programming side, and it includes a darker color for the grey windows where File and everything is, I would be one happy customer and I'm sure others would be too.
Thanks for taking the time to read my suggestion!
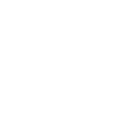
program mode mouse button combo for end feature
In program mode, programming on cad, create a mouse button combo that would create the feature instead of having to hit end on the keyboard
Maybe left + right mouse button clicked together
Сервис поддержки клиентов работает на платформе UserEcho