Hexagon Measurement SystemsNo matter what Hexagon measurement equipment or software you use, we want to hear your ideas and suggestions on how we can improve.
Thanks for your assistance in helping us shape the future. |
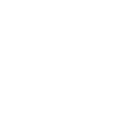
Automatic Set Search Path
I am updating from 2015 up to 2024. I have several machines with different probing systems, saved alignments, etc. Each machine has its own folder with all of its programs. I just discovered the 'Open' tab when I open PC-DMIS.
Every time I need to go into the programs for a different machine, I have to remember to change the 'Set Search Path' options. It does not work well after I have a program open, so I have to close it, set the path and then open it again. How about a way to set each folder with its own predefined 'Set Search Path'?
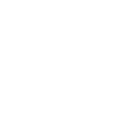
Recognize whether or not a feature exists on the part with scan data.
A lot of times, features are reference on drawings and just need to verify if they exist or not. Basically "is the hole there or is it not". This could be done pretty easily with Scan data and a CAD model to verify if features were manufactured properly without having to use actual probing. This specifically would work very well for an Arm, AS1 and PC-DMIS. It would be pretty simple to add to the feature settings instead of extraction, to just verify a hole/slot or whatever feature is there.
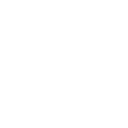
Save the PC-DMIS version/SP/Schema so that we can identify what version of PC-DMIS is needed to open this file.
Can we get some way to record what version/schema of PC-DMIS is required to open a particular PC-DMIS file? With the rolling cutoff and some users having a mix of schema for their routines, I fear difficulties with using the migration utilities in the future.
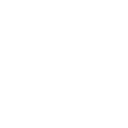
Missing evaluation form requirements with rectangular type
Missing evaluation form requirements with rectangular type by Iso Std
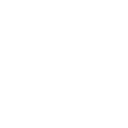
Allow evaluation of angularity and perpendicularity vs 3 datums and MMC/LMC modifier to said datums with ISO1101 settings
Hi PC-DMIS team and users.
I have time to time encountered requirements that call out for angularity and perpendicularity versus 3 datums. Since PC-DMIS currently doesnt allow this, i have researched about it with my local PC-DMIS provider (Hexagon Sweden) and my employers ISO experts, who are part of the ISO committee. According to both Hexagon Sweden and the mentioned ISO experts, both perpendicularity and angularity, although not very clearly described in ISO1101 currently, are fully intended to be used with a complete datum system such as A B C, which is confirmed with the people who participated in writing the current version of ISO1101.
It is to my understanding that this would be equal to, or very similar atleast, to be using surface profile with a complete datum system but with the OZ modifier applied. This is my current workaround when i see such requirements on flat surfaces. But when the requirement applies to a bore
or a shaft, this workaround no longer works and i have no proper way to do it.
In addition to implementing a change like this, a yellow text warning, similar to the warning text to [DF] modifier could be used as soon as the 3rd datum is defined. Where the text implies that a 3rd datum for angularity and perpendicularity is not clearly described in ISO1101, and also asks the user to consider if this is really the intended requirement for the feature, or something along those lines.
In addition to this, bring back the ability to add the LMC and MMC modifier for the datums used for the angularity/perpendicularity evaluations. There is nothing stated that prohibits this in current standards. It is allowed for surface profile with OZ modifier, so after all, why shouldn't it be allowed to be used for angularity and perpendicularity.
If you need any further clarification or explanation, im happy to fill in. Thanks!
Below are 2 example pictures from the same technical drawing.
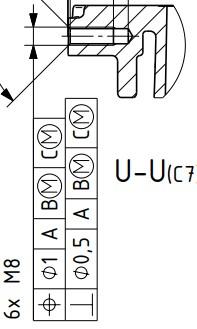
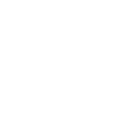
Add Length of Cylinder to the Measurement Strategy Editor and Quick Features Widget
I want to be able to set the length in the Measurement Strategy Editor as well as in the Quick Feature Widget. If the length was included when copying parameters, that would also be helpful. It just seems like cylinder length has been disregarded. We use a lot of cylinders for our hole locations, and sorry to say but the void detection still makes the probe go down too far and it rubs the bottom face. Our threads also do not go the full length of the drilled hole depth, so void detection just doesn't work too well for these features.
Customer support service by UserEcho