Hexagon Measurement SystemsNo matter what Hexagon measurement equipment or software you use, we want to hear your ideas and suggestions on how we can improve.
Thanks for your assistance in helping us shape the future. |

Hybrid best fit alignment
It would be great if it was possible, in a best fit alignment, to either be able to 1) specify some feature as least squares and some features as vector least squares or 2) in the least squares have the ability to select vector also ( i.e. XYZT ) so one could exclude all but T and lock only that feature by it vector.

Search Path for Excel Form Report Template
Excel Form Report Templates should have a search path designated by the user. At this time, the templates are version specific and do not carry over to newer versions. You have to copy the template and corresponding layout.xml file from one version to the next.

Add: Insert link (web)
I would like to add a clickable link to the start of our program which will open the browser and navigate to the intranet address where the model and drawing are. We will have a quick access to the latest model and drawing without going through a couple of folders...

Create or Edit Report and Label Templates from Home Screen
Dear PC-DMIS,
I would like to be able to open Report or Label templates directly from the Home Screen.
Now i have to open a measurement program and only then am I able to create or edit a Report or Label template.
It would be easier and faster if I could open such a template directly from the Home Screen.
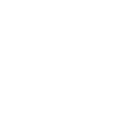
Smart Measurement Strategy Editor
Improve the MSE by letting the strategy vary based on nominal Cad conditions. For example, when a cad inside circle diameter matches the minor diameter of a common thread, change the pitch in auto-circle to match that thread. Probably would be best to make this generic rather than hard coded and being able to test multiple conditions would be very nice.

Adding a block tolerance widget and display precision to the dimension block
When trying to dimension features I would like to have a radio button in the box to keep from typing displayprecision when matching a print. Also adding a block tolerance widget so when you click the radio button the tolerance automatically adjust to the block tolerance. This would keep you from typing the tolerances each time for non critical features which is about 90% of prints.
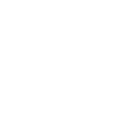
Construckt sphere in cone
We measured an inner cone as an element and want to construct a ball with a fixed diameter of Ø19 in the cone (see picture). The goal is to determine the distance of 25.1( see Picture). Currently we construct a circle (Tangent) into two lines.

Probe head B angles only
This is a hardware request only.
I'd like to have a probe head with only B angles for rotation of star probes.
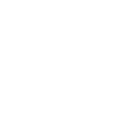
copy and paste with pattern that CAD would be pasted the same way as routines.
once the routine is programed on original CAD, the copy and pasted procedure should include an option that "want to copy and paste CAD" the same way as routine so that CAD would be synced with routine. with this way, it would be easy to modify or add feature based on current run. for now after running all parts with pattern (many parts on a fixture), if i go back to add one feature on CAD number3 for example (CAD number 1 is original) at location 4, coordination of new added feature would not be correct anymore because CAD number 3 is not synced with the routine at that location, location 4. at location 1, CAD would be synced with routine but not other locations. thus it would be a big improvement on "copy and paste" if CAD and routine can sync automatically any location.
Customer support service by UserEcho