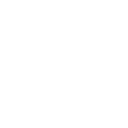
0
Optical flatness measurement
We often have to measure very small optical flatnesses on contact surfaces.
Here it would be useful if I had to Focus with once window only.
Simply define the measurement window and the division of the measuring range analogous to the measuring method from Werth GmbH.
Customer support service by UserEcho
Wolle,
Would this be measuring multiple points at one time?
Yes, see quote:
In 1999 presented a method that is based on the principle of focus variation. With this Werth 3D patch and today's image acquisition technology, it is possible to capture several hundred surface points in a few seconds at the same time. Maschinelle Übersetzung
That is very interesting. I've done multiple tabs or contacts like this. One thing I have noticed however, the focal accuracy is much higher with a smaller FOV. I believe this is because the depth of Field is decreasing as the FOV is decreasing.
The shallow depth of field is very important for accuracy.
But if I can measure the flatness of an area from 0.5 x 0.5mm at a focus, because I capture multiple surface points at the same time, I save a lot of measurement time!
Agreed, people tend to have the conception that vision is faster than contact... Which is true in volume of points, but not with focal measurements. Could be really neat to see.
Neil,
Is this something that is possible? I haven't done a lot of research on Werth and Hexagons relation ship - but the technology could be really interesting to develop and would also allow for 3d oriented objects to be measured (i.e. measuring a semi-circle who's face is perpendicular to the z-axis of the machine, or tooling balls)
Hi Kyle & Wolle, I am not familiar with the Werth method, but if I understand correctly, you would like the ability to define a focus area and a grid of points in X & Y ? I have seen similar requests from the Electronics Industry, Do you have other applications? If you do, please let me know as this would help me understand the potential benefits this could provide.
Would you also expect this to be available on planar surfaces which are parallel to the camera?
Thanks,
Neil
Hi Neil,
thanks for the request.
Our application would be flatness measurement of very small contact surfaces. The typically, plane size are 0.2 x 0.2mm - 0.4 x 0.4mm
Hi Wolle
Thank you for your reply. My team is currently busy working on a number of hardware related items but I will create an entry in our system for future consideration - PCD-169722
If this item is scheduled in the future it would be great if you would agree to be a stakeholder and provide feedback throughout the development.
Neil,
I think I understand your statement, but in my mind effectively this would allow every pixel in the focus to be tracked with a 'focus' parameter (almost like a scan) and it would actually have x,y,z coordinates. From this you would be able to get 'topographical map' effects as well as several (probably hundreds if not a few thousand) focus hits in one movement.
This would speed up a lot of measurements on small electronics surfaces, that albeit small, still manage to have a flatness callout.
Perhaps it would be registered as a focus scan feature, starting from the pixel in the upper left corner and moving left to right, top to bottom. Then if you could apply point cloud operators and filters based on 3d geometry as well as several scans of a single feature? Than the above cylinder half could be measured with representative 3D geometry?